What exactly is involved in Vaer's USA watch assembly?
Updated
by Vaer Watches
In this article, we're going to provide an in-depth breakdown of every step involved in our American assembly process.
We've been talking about American assembly for years and it's one of the most central aspects of our brand, so we're really excited to pull back the curtain a bit more and show everyone exactly what "assembly" actually means.
We love to share the fact that we do American assembly but the statement alone doesn’t share the whole picture. It feels like we’ve responded to hundreds of comments over the years from folks who think American assembly simply means attaching some springbars and straps - if you’re one of those people, you’re going to be in for a pretty big surprise at just how complicated and involved the process actually is.
1) Pre-Assembly
One of the most important steps of the assembly process is pre-assembly, which mostly involves getting organized. The first step of that is actually sorting and receiving components in packages and then kitting them. That really involves opening boxes and preparing matching sets of components - grouping cases, crowns, dials, hands, and movements together by the corresponding line and model.
Once those things are kitted and organized, one of the first things that we do within the United States is to build what we call "SCC", or stem-crown-combos. When prepping crowns and stems for a watch we have a specific size that every single stem needs to be cut to. This step is very important as if the stem is cut too long or too short it will throw off the action of the crown and the crown's ability to either screw all of the way into the case or effectively pull out of the movement.
While this step could be done by hand and in the early days we did do it by hand, we now use a machine that enables our technicians to replicate exact cut lengths at scale. The process by hand is incredibly meticulous and time-consuming, and this machine is one of many efficiencies that our team has created over time in order to improve the overall process.
While this machine looks awesome and is a really neat thing to watch and see, it's also a really great first stage of the assembly process to serve as a reminder of why American Assembly is so challenging.
In many cases, these machines don't exist in the United States - they're not made here nor are they easily accessed, so it's really difficult to build up an effective assembly facility when the lack of critical infrastructure isn't here - this is just one small machine that can be seen as critical infrastructure in the watch assembly process. If you were to take a look at the watch industry in Switzerland or Japan, you'd find something like this to be much more commonplace.
An important note is that the pre-assembly and kitting process is all done outside of the actual assembly room, in order to reduce any exposure to contaminants from the shipping process - tiny debris from shipment packaging can cause a headache in the assembly process, so all of this is kept separate from the environment where watches are built.
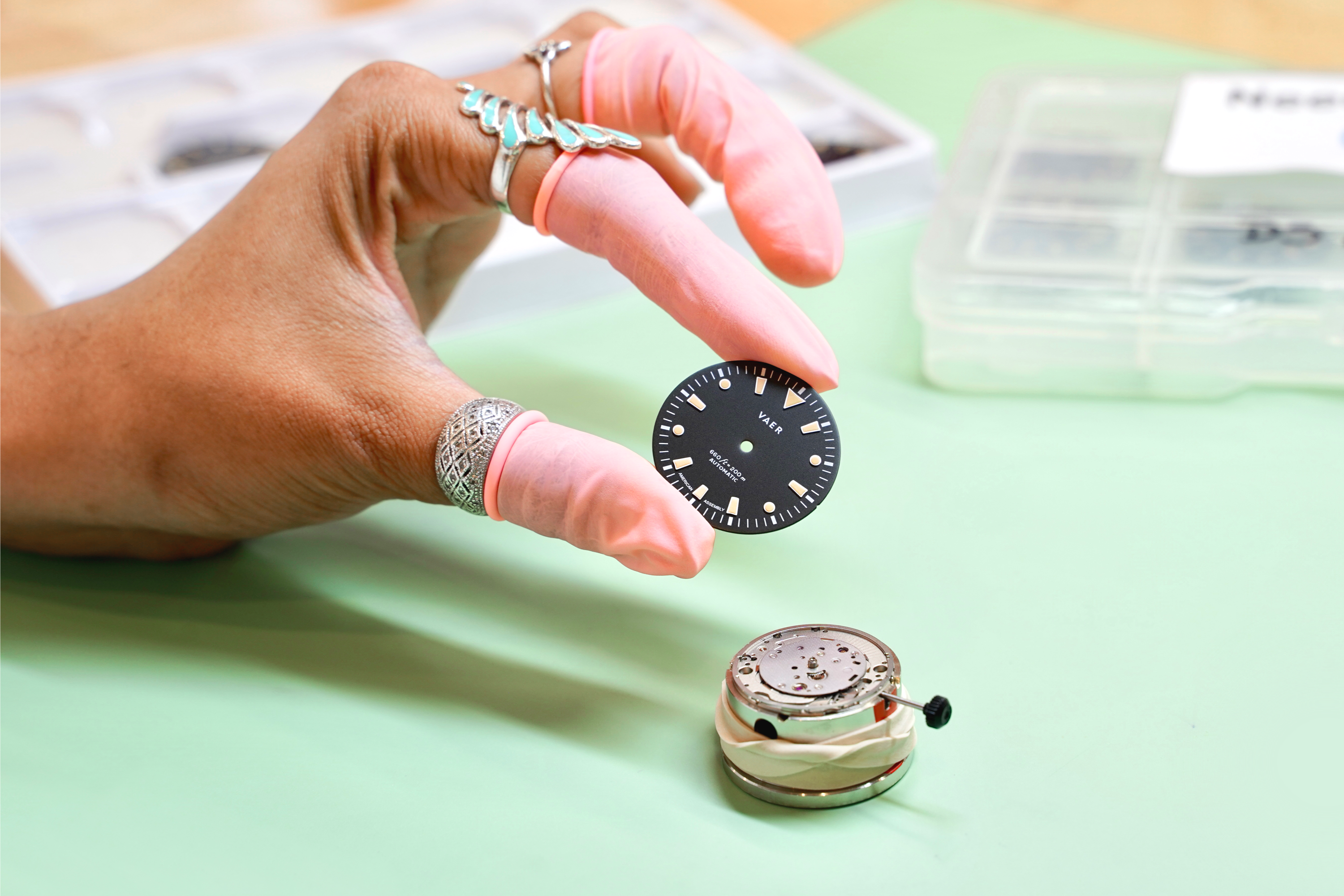
2) Dial and Movement Assembly
The actual assembly of watches takes place in a temperature-controlled clean room with laminar airflow. Technicians are also required to wear lab coats and specific footwear to further reduce any external contamination. While these steps may seem like overkill to some, we see them as necessary. Assembly is the final, critical step to bring together a set of intricate pieces that have taken months to produce. Our team has spent time and money to invest in the equipment and processes to compete with the best standards in the world, and it's something we're incredibly proud of.
Next up, we're going to jump into the first steps of the actual clean-room assembly - specifically the dial, and hand installations. We'll also provide some details around our quality control or QC process, and why it’s so important to our manufacturing process in general.
Once we enter the air-controlled clean room, the first assembly stage is going to be attaching the dials to the watch movements. In many ways, a watch movement is like the engine of a car, and our assembly process is basically a series of steps building around this engine.
- Reagan Cook, Vaer Co-Founder
In terms of the dial assembly, the tech will have two trays on either side of their station, one with dials and the other with movements. In order to attach the dials, the technician needs to remove very small screws from the movement, position a circular dial spacer under the dial, and then re-install the screws locking the dial in place.
Unlike a lot of retail industries, where huge margins are baked into the cost of goods, and most raw components are seen as pretty disposable, at Vaer, the parts and pieces of each watch are extremely valuable and take months to produce. A small smudge or a scratch at this final stage could cost the business hundreds of dollars and so caution and control are incredibly important.
The ability to maintain control over such small components, while working efficiently at scale takes real talent. If you’ve purchased one of our watches in the past, hopefully, you’ll feel a small sense of pride in helping to support this type of craftsmanship with a new generation of watchmakers.
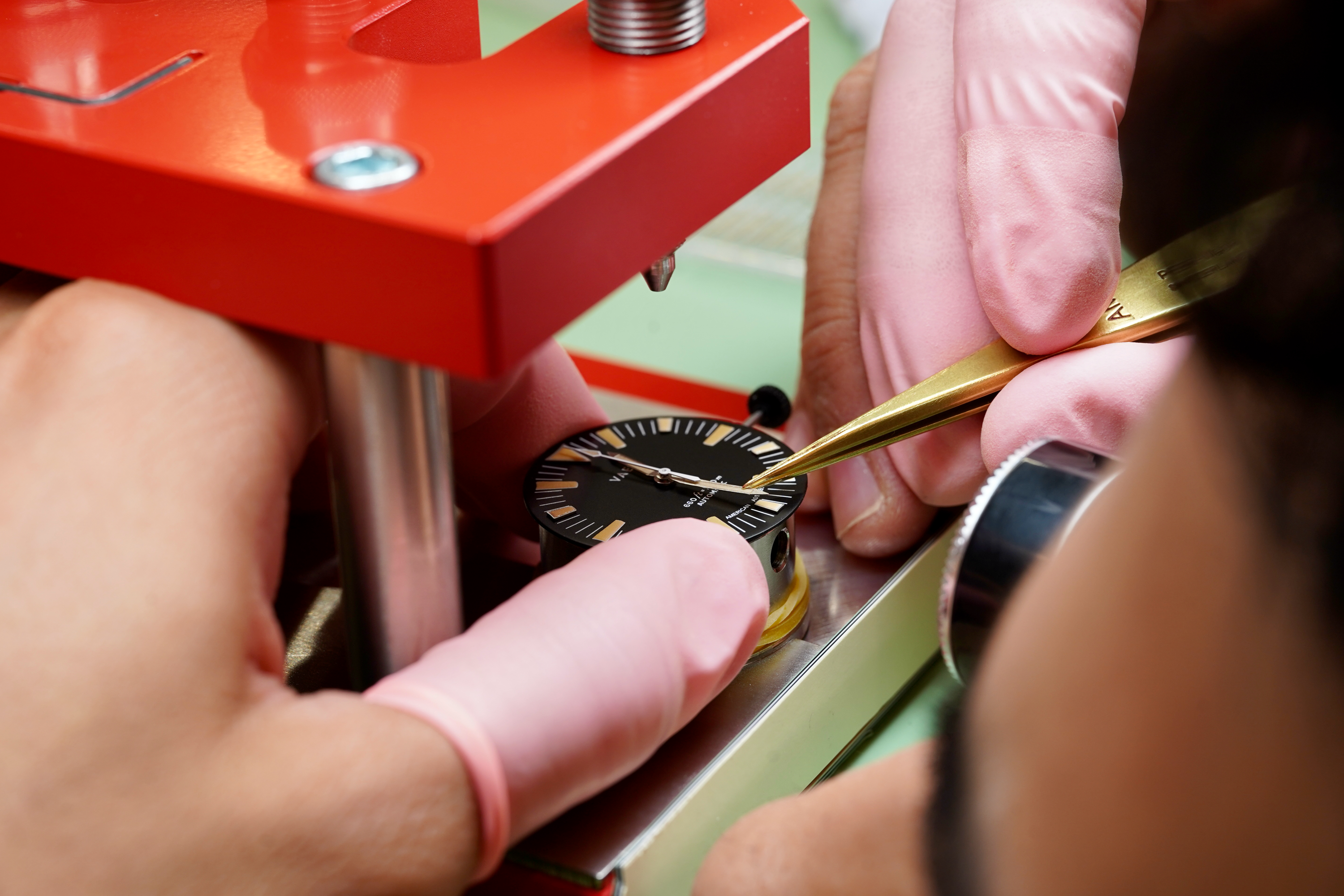
3) Hand Assembly
Once the dials are attached to the movements, they are set in a tray for the first assembly QC check. QC is done for the same reason we use a cleanroom, lab coats, air filtration, and finger cots - making mistakes with US assembly costs a lot of money.
Supporting American sourcing means supporting American labor - and compared with China, it’s pretty darn expensive. Based on hourly assembly costs, 1 minute of assembly in the United States, costs about the same as 30 minutes of assembly in China.
QC helps us catch issues early and make the most of our technician's time. The type of issue that might be caught at this stage, might be finding a very small fiber embedded under a dial index. This watch would fail QC and be cleaned before moving on to the next stage, which is hand installation.
Installing the hands of a watch is definitely one of the more challenging steps of our assembly process, and basically involves stacking the hour, minute, and second hand onto a very small pin protruding from the movement, through the center of the dial called a pinion. While it’s impossible to see without magnification, there’s a microscopic ball joint at the end of the pinion that the second-hand locks into.
Once the hands are installed, the tech will test out the hand alignment by rotating the stock factory crown, and make sure that the hands are aligning properly so that there isn’t any friction or tension between the hands and the raised indexes. The technician will also work to ensure the hands are sitting as straight as possible and are completely perpendicular with the pinion. The friction from poor hand alignment can put undue strain on the movements, and ruin a watch's accuracy over time. For this reason, the added checks and inspections done at this stage are incredibly important for both the aesthetics and technical performance of the watch.
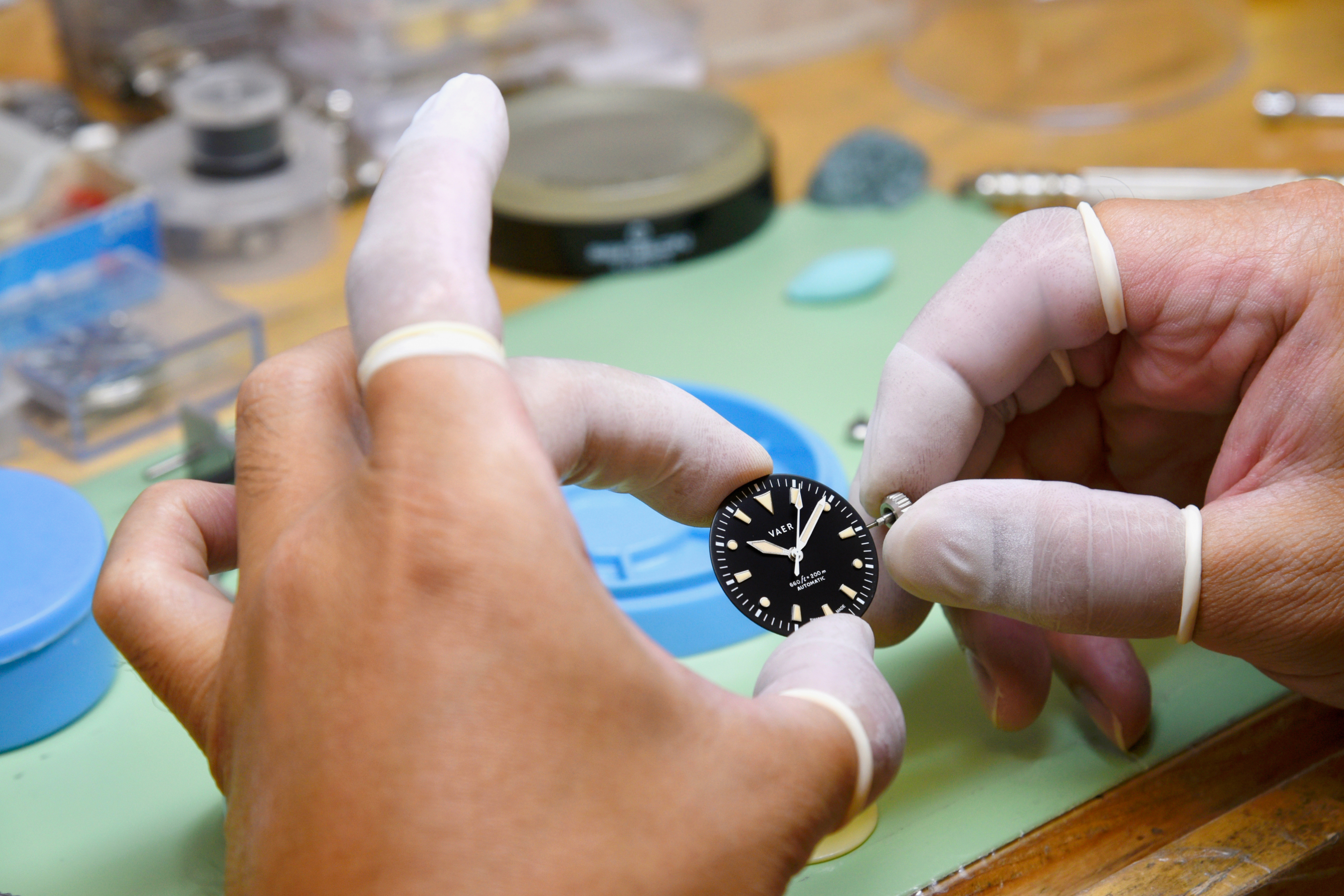
4) Case Assembly
Once the dial and hands are properly installed on the movement, we've essentially created a working time-telling device. The remaining assembly steps are about protecting the movement and dial and making sure it will keep accurate time through extreme outdoor conditions.
You can have the best interior components on the market, investing in a movement that costs hundreds of dollars, but if you have a poorly assembled case or faulty gasket the entire watch will be compromised in real-world usage.
At this stage, the technician works to insert the movement and dial through the open back of the watch case. This technique is commonly referred to as back-loaded assembly and is the standard practice for quality watchmaking because it allows for the entire watch to be removed through the case back if repairs are needed down the road.
Many mass-market fashion watches and luxury brand knockoffs avoid back-loading cases because they're more expensive and they require a more sophisticated case design. Instead, they tend to "top load" their cases, dropping everything through the dial, and installing the glass crystal as a final step.
The problem with this approach is that you need to break the crystal to repair the watch, making top-loaded watches "throwaway items" meant to be replaced rather than repaired.
Obviously, that's not our vision for Vaer. We build our watches to last for decades and a big part of that means that they need to be easy to repair and maintain.
In addition to the backloading design, our rigorous water-resistance standards add additional requirements to the casing stage. Both our 10ATM and 20ATM watches use screw-down crowns and casebacks, and leverage extra-thick rubber gaskets at all openings to ensure an air-tight seal.
Near the conclusion of the casing stage, the technician will re-introduce the stem-crown combinations. Once these are attached the watches are essentially complete, and only need to pass a final QC, water-resistance testing and for our automatic watches, time rate testing, and regulation.
5) Time-Testing
While a flawless assembly is critical, ultimately, owners are going to judge their watches based on how good they are at telling time. Our C3 and C5 quartz watches, which are powered by the US-sourced Ameriquartz movements offer near-perfect accuracy, with a standard rating of -10/+20 seconds per month.
Mechanical automatic watches like the ones seen in this video, and preferred by the luxury watch industry, are far less accurate. Even $100,000 movements, used in the rarest Swiss concept watches are rarely capable of surpassing Swiss Chronometer or COSC certification of -4/+6 seconds per DAY. For that reason, movements need to be tested and regulated at the assembly stage to ensure they offer a competitive timekeeping standard.
Our USA assembled automatics like the D5 models shown in this video are all guaranteed to -5/+15 sec / day. It's important to keep in mind that this is the outer bounds of our regulation standard, and many of our automatic watches achieve and surpass the standards for a COSC grade.
While COSC is seen as the gold standard for mechanical accuracy, in many ways it's really just a marketing label for Swiss luxury brands. The certification alone costs hundreds of dollars, which is why almost all value-oriented microbrands opt to handle regulation in-house. That said, a COSC-level Vaer regulation standard is something we may introduce on higher-priced models or as an optional additional cost in the future.
6) Water-Resistance Testing
Once the watches are guaranteed for accuracy, the final step of the assembly process is water-resistance testing. There are a variety of ways to test a watch's resistance rating, and interestingly, few of them involve the use of any water. Instead, the most common method is a dry pressure test which uses sophisticated equipment to artificially generate extreme air pressures inside a vacuum.
From our own experiences with overseas suppliers, the water-resistance ratings provided by Chinese manufacturers often fall short of their stated ATM rating. Not only do they often lack the top-tier testing equipment, they also tend to test watches by pulling a few samples out of a larger batch. While this CAN work if you have limited expectations around in-water use, for Vaer, use in the water is a critical aspect of our product value, and testing each piece ensures that our owners can be confident in and around the water.
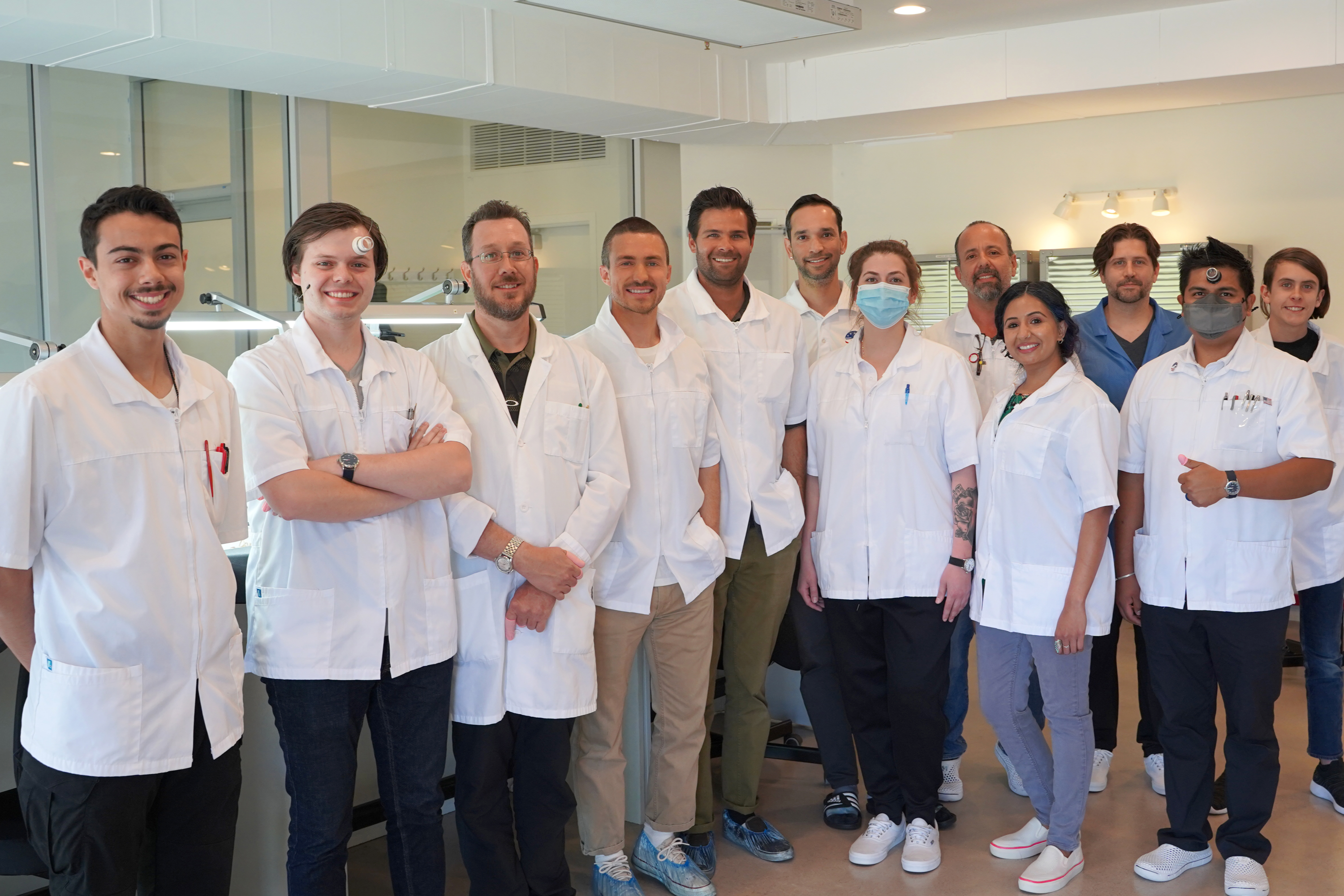